Oilfield Testing
Ensure Operational Efficiency, Safeguard Environmental Health, and Maintain Compliance With Industry Regulations
Oilfield testing is a crucial aspect of the oil and gas industry, assessing the properties, quality, and safety of components involved in drilling, production, and refining processes. These tests are essential for ensuring operational efficiency, safeguarding environmental health, and maintaining compliance with industry regulations. The tests involved in oilfield testing include crude oil quality analysis, water content analysis, gas content analysis, corrosion and scale analysis, scale formation test, drilling fluid analysis, rheological tests, and reservoir fluid analysis.
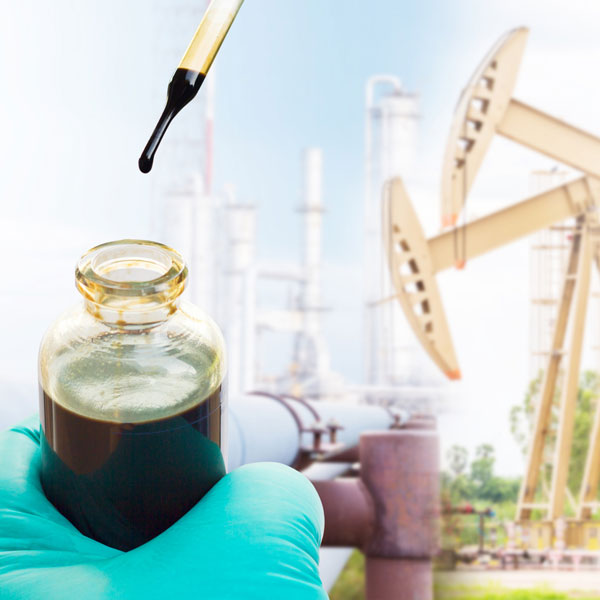
Why Oilfield Testing Is Crucial
The importance of oilfield testing in an environmental lab lies in its benefits for operational efficiency, environmental compliance, resource management, infrastructure integrity, safety, regulatory compliance, and data-driven decisions. Accurate testing ensures that components like crude oil, gas, and drilling fluids meet specifications, optimizing extraction and refining processes. Rigorous testing prevents the release of pollutants, contaminants, and hazardous substances into the environment, safeguarding ecosystems and public health. Efficient testing helps manage resources, minimize wastage, and ensure the longevity of pipelines and equipment. Proper testing minimizes the risk of accidents related to pressure imbalances, gas leaks, and equipment failures.
Oilfield testing in environmental labs plays a pivotal role in the oil and gas industry’s sustainable and responsible operations. By assessing the quality, safety, and environmental impact of various components, testing ensures efficient, safe, and compliance with industry standards and regulations.
Common Tests for Oilfields Include:
- ASTM D287 – API Gravity
- ASTM D2711 – Demulsibility
- Dynamic Demulsibility (DDE)
- ASTM D972 – Evaporation Loss
- ASTM D92 – Flash Point
- ASTM D4809 – Heat of Combustion
- ASTM D6304 – Water by Karl Fischer
- ASTM D5800 – Noack Volatility
- ASTM D943 – Oxidation Stability
- ASTM D4310 – Sludging and Corrosion Tendencies
- ASTM D2070 – Thermal Stability
- ASTM D445 – Viscosity
- ASTM D2500 – Cloud Point
- ASTM D4052 – Density
- ASTM D892 – Foaming Characteristics
- ASTM D3520 – Magnetic Quenchometer
- ASTM D665 – Rust Preventing Characteristics
- ASTM D3705 – Misting Properties
- ASTM D4636 – Corrosiveness and Oxidation Stability of Highly Refined Oils
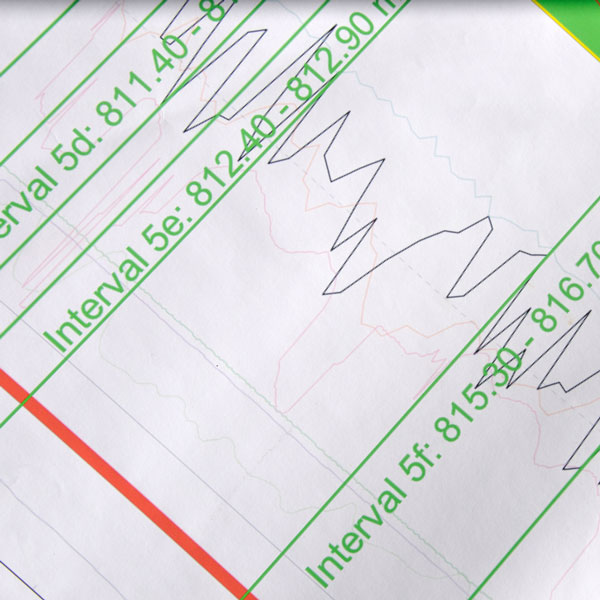
Fuel Testing:
- ASTM D86 – Distillation
- ASTM D5191 – Vapor Pressure
- ASTM D6371 – Cold Filter Plug Point
- ASTM D2276 – Particulate Matter
- ASTM D2500 – Cloud Point
Oil & Grease Testing:
- Grease Compatibility – D6185, D217, D2265
- ASTM D1742 – Oil Separation
Coolant Corrosion Protection:
- ASTM D7820 – Coolant Corrosion Protection
- ASTM D1384 – Corrosion Test for Engine Coolants
- ASTM D1120 – Boiling Point of Engine Coolants
- ASTM D1121 – Reserve Alkalinity of Engine Coolants